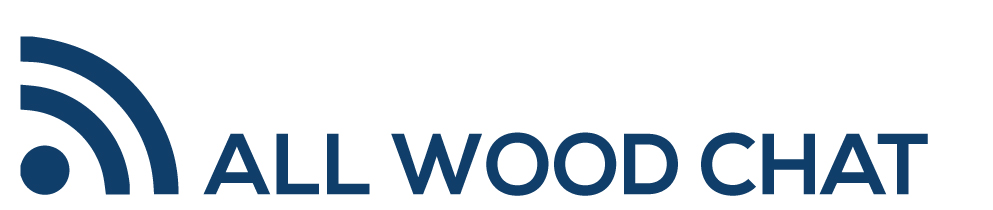
Theo Haralampou or 'Theo the Woodturner', tells us about his passion for woodturning, his journey with it and where beginners should look to start. Theo is based in Brisbane and regularly hosts free demonstrations at Carbatec's Brisbane store.
Throughout this podcast you will hear about Theo's journey to woodworking, what inspires him, the projects he is most proud of, the future of woodworking and he gives insightful tips for those looking to make their start in woodturning.
|