The pocket hole joint’s simplicity and strength are two of the many advantages over any other non-structural joint. Integral joints such as mortise and tenon joints, finger joints and dovetails are far superior and more decorative, but for many hobbyists and professionals alike, forming these joints can be very time consuming at best and in many cases, unnecessary. Non-integral joints (biscuit joints, dowel joints and the like) can be quick to produce, but they call on a fairly high skill level to perfect, and without this standard of production are frequently ineffective. For example, a dowel requires perfectly aligned holes on two separate workpieces. Misaligned holes mean misaligned work, which in turn means more sanding, scraping and colourful language. Biscuits joints are somewhat easier to form and by design they offer a small margin for error. They rely heavily on gluing to form an adequate bond, but this makes them unsuitable for many joints that have stress applied to them. Here's a good example of the pocket hole jig's merit in creating strong joints for a solid, functional workpiece. Our project this month is a handy little footstool that will be a great addition to any home: use it in the kitchen for gaining access to the back of the pantry, in the laundry, in the bathroom or even in the workshop. The design is extendable enough that it can be modified to form many other furniture pieces, just by changing the dimensions. It can be used as a starting point for a coffee table, or if you get a little more adventurous, even a dining table. Remember, it’s just a matter of joining the thinner panels together to make wider panels for wider jobs. We will be producing all our joints with the Kreg K4 Pocket Hole Jig. There are many other pocket hole jigs in the Kreg range that will work just as effectively, but they may require a few extra steps. The advantage in using the Kreg Pocket Hole Jig, is that it produces a simple, strong, structurally sound joint. It’s perfect for this and many other applications.
Materials you'll need: The first thing you'll need is the Project Plan.
CLICK TO DOWNLOAD PROJECT PLAN (PDF) You’ll need five pieces of timber. We used Tasmanian Oak for our stool. Pine works just as well but may require staining to give a more decorative finish. High grade ply can also be used if there are not too many gaps in the layers. If you don’t have the machinery to size and dress this yourself you can pick it up from your local timber merchant pre-machined, or you can adjust the sizes to match what you can easily source. > 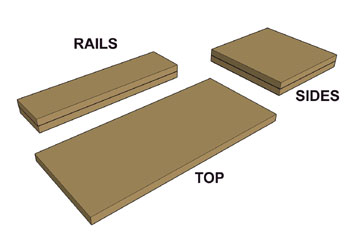 | Your starting materials. Hardwood, softwood or suitable plywood. | |
Sizes below are for boards machined to a ‘ready to finish’ state. (fig 1 image) 1 x top - 500mm x 220mm x 19mm 2 x sides - 250mm x 250m x 19mm 2 x rails - 410mm x 105mm x 19mm In addition to your wood, you'll need - Kreg K4 pocket hole jig KR-K4MS (or similar Kreg Jig)
- Kreg Square driver bit (included in KR-K4MS)
- 18 x 1¼” Kreg® pocket hole screws (Coarse thread (KR-SML-C125-100) for softwoods and manmade boards and fine thread (KR-SML-F150-100) for hardwoods)
- a router bit with a 3mm (1/8”) 838-190-11 round over bit and bearing
- a router with 1/4" collet (Triton TRI-TRA001B)
- a jig saw or coping saw
Cutting the Curved Profiles The first step is to cut the profiles into the top, sides and rails. I found the easiest way to mark the profiles on the sides and rails was to print the profiles I wanted onto A4 paper then glue the paper onto the boards and cut them out with a jig saw. The paper can be easily removed in the finishing stage. Remember to run the pattern along the grain of the timber. I know this sounds basic, but I have fine examples of how NOT to cut timber in my workshop (if anybody would like to see). Carefully cut all sides and rails as shown on your plan. The round corners on the top can be achieved by marking the desired radius and carefully removing the waste with a jigsaw, coping saw or by sanding off the waste on a disc sander (the disc sander is the cleanest method). Most woodworkers choose a 5c or 10c piece to form their corner rounds. That’s usually all they can afford! 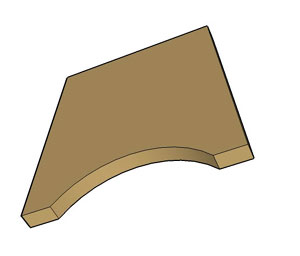 | 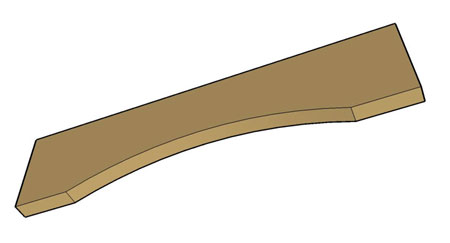 | Side with curve cut | Rail with curve cut |
Routing a 1/8" Round on the Edges A good idea is to mark the top edge of the side panels and the top & side edges of the rails with a chalk or pencil mark. This will help identify the parts we DO NOT want to rout the edges on (see diagram below): 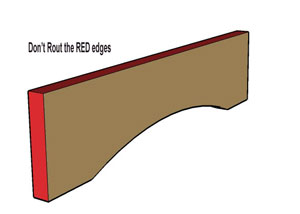 | | 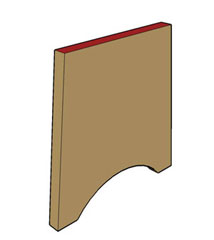 | Rail with edge marking to avoid routing... | | ...and the side piece also. |
Routing a 1/8” round on most exposed edges gives a nice and soft finished look, and will prevent splintering along these edges. Too large a roundover on such a small item will look disproportional and could look very unprofessional. Less is more. Remember, DON’T rout the areas we have marked earlier.
Sanding the Components Give every component a good sanding through the grits. I recommend 80, 120, 180, 240 and 320. A random orbital sander (Bosch BO-GEX125-1AE) makes light work of the large flat surfaces. I found that sanding the profiled sections with a drum sanding set in my drill press for the coarse grits first and then by hand for the finer grits allowed me to give them the extra attention they needed after being cut out with a jig saw. Sanding by hand is always possible if you feel like a workout. Being careful at this stage will make a lot less work after the stool has been assembled, and the finish quality will be far better if you have worked your way through all the grits without skipping a step. Just try it, and you will see the difference.
Joining the Components Finally, you get to use your Kreg Jig! Step 1: Set out the components as they will be when complete, much like a “dry fit” (Fig 1). The extreme adaptability of the Kreg Pocket Hole joint now comes into its own. You can lay out the stool and decide the position of the components (flush with outside edge or set back from edge) - the making of the pocket hole is remains the same. We have positioned the pocket holes on the inside of all components so that they are not seen. Alternatively, you can have the holes exposed on the outside and then plug them with one of the many Kreg Pocket hole plugs. Step 2: Simply mark the pocket hole centres’ positions and drill all your pocket holes on your rails and sides as shown in the pictures below. Remember to drill the pocket holes on the sides close enough to the centre to keep them hidden when the rails are attached. Follow your Kreg Jig instructions to determine the jig setup and bit depth. Remember that you only need to drill one side of your joint. That’s why you brought a Kreg Jig, isn’t it? Step 3: Now you can assemble the components, by repositioning, clamping (there are many specific Kreg clamps to help this operation) and driving the screws in. Remember to tilt the stiles to the angle on the outer edges of the sides. I attached the sides to the top first (Fig. 4-1), then the rails to the side (Fig. 4-2), but you could just as easily assemble the entire sub-frame (sides and rails) and then attach them complete to the top. 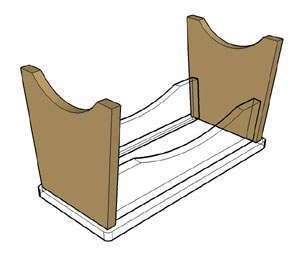 | | 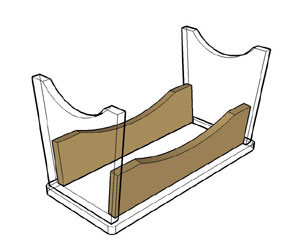 | (Fig. 4-1) Attach the sides first... | | (Fig. 4-2)... then the rails. |
I didn’t use glue in building our footstool. It’s not required, but it may be added if you like. If you do, remember to wipe of the excess before it dries and before finishing.
Finishing Two or three coats of Danish oil (Liberon LBN-014642 - 500ml) will give the stool a nice, natural finish. This can be applied by hand and rubbed in well. Burnishing will give a higher gloss level. Burnishing can be done by rubbing the oil in with 600 and 1200 grit wet and dry sandpaper. Build up the heat with the sandpaper to complete the burnishing process. Once burnishing is completed (two or three coats), the footstool should be dry. If it’s not, then you need to rub a little harder and longer. Obviously you can lacquer or clear coat the footstool, but this will require some more equipment and time for drying.
How long until you can use your new footstool? Once it’s dry, immediately! That’s the advantage of using the Kreg® system. It’s strong enough to use straight away. 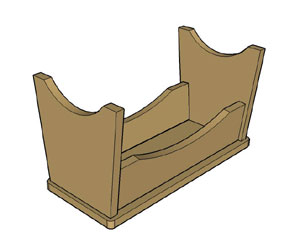 | | 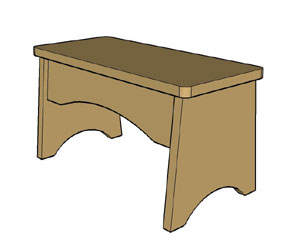 | The finished product, from the bottom... | | ...and the top, ready for use!... |
|